Occupational Health & Safety
Policy on Occupational Safety and Health
Based on its stance of respecting human life and ensuring safety, as laid out in the Group Corporate Philosophy and Corporate Stance, the Yamato Group thoroughly adheres to its philosophy of placing safety first and business second, positioning respect for human life as a priority at all times.
Occupational Safety and Health Management Regulations
The Yamato Group has provided occupational safety and health management regulations to each Group company. The purpose of the regulations is to set out necessary matters related to safety and the health of employees based on relevant laws and regulations, such as Japan’s Labor Standards Act and the Industrial Safety and Health Act, to enhance safety and health activities in the Company, to clarify the necessary basic matters for preventing occupational accidents, to promote the creation of comfortable workplaces for employees, and so forth. The safety and health management regulations include six items: Safety and Health Committee, Safety and Health Management System, Safety and Health Plan, Safety and Health Education, Health Management, and Safety and Health Standards.
Yamato Transport Safety and Health Management Regulations (Japanese only)
Promotion Structure
Yamato Transport has established a Central Safety and Health Committee, chaired by the executive in charge of occupational safety, to deliberate on necessary matters for safe business activities, such as safety and health and traffic accidents. In addition, safety meetings and Safety and Health Committee meetings are held at each regional branch and business office
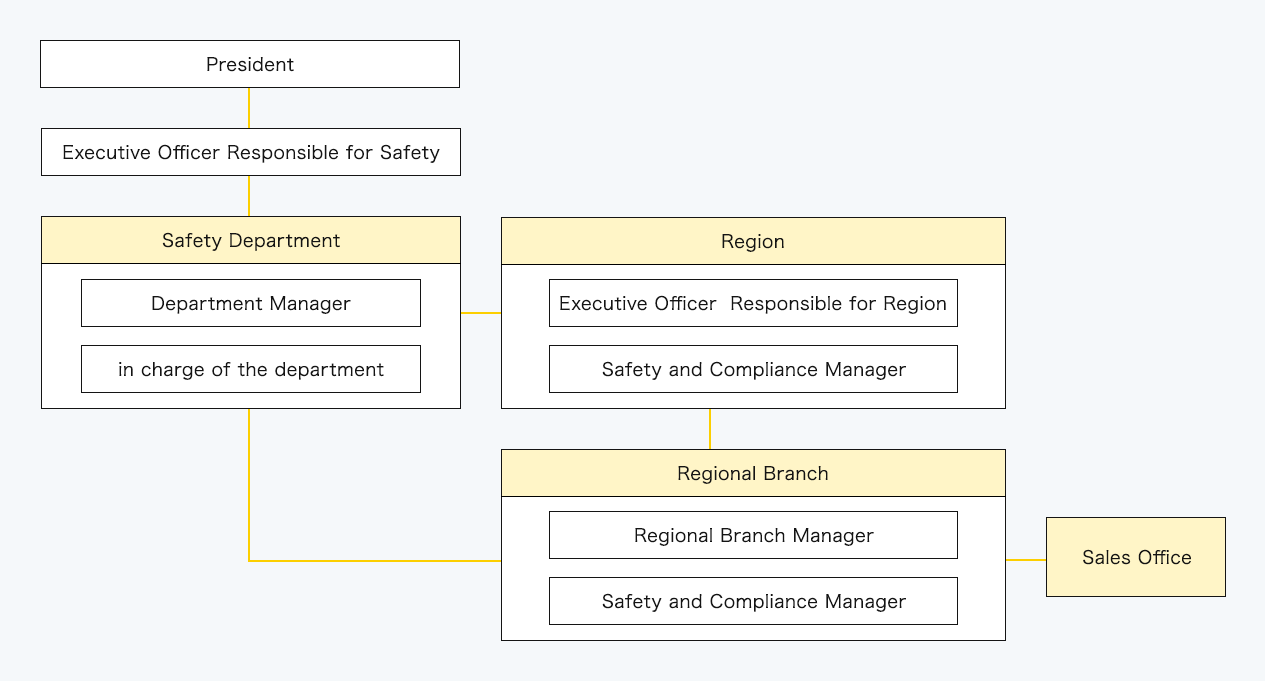
Initiatives Related to Safety and Health
To embody the concept of safety first, business second, we are promoting the construction of secure, safe working environments by increasing the level of workplace safety and health in preparation for the introduction of the Occupational Safety and Health Management System (OSHMS).
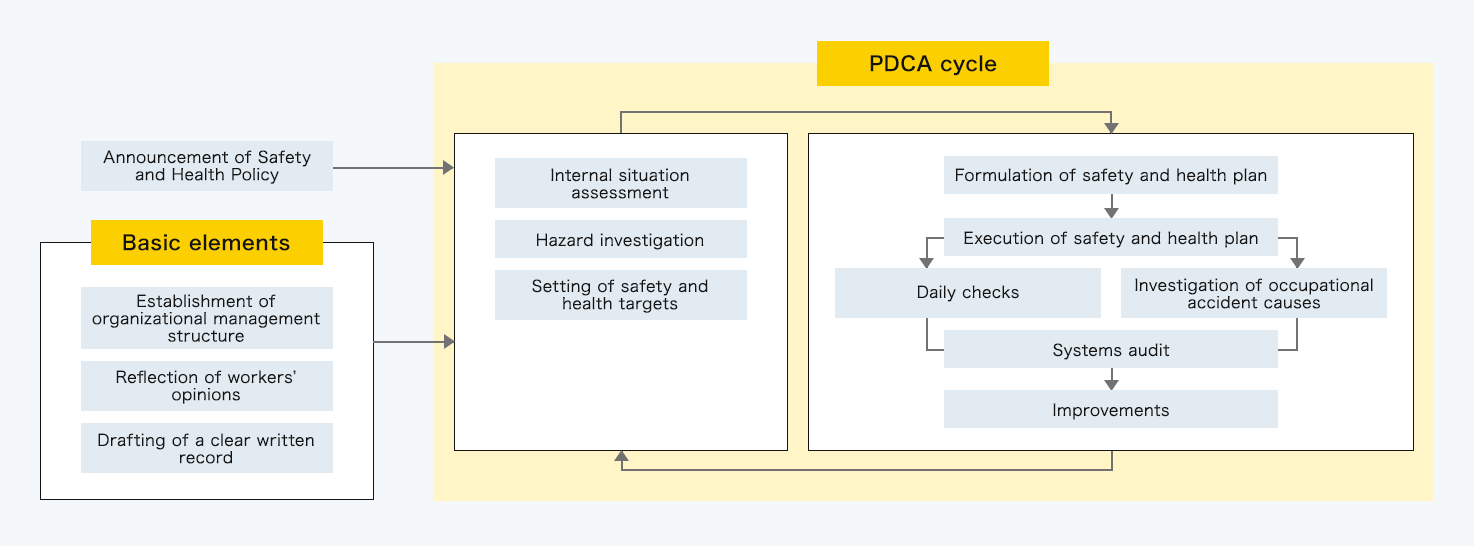
Creating a safe and secure work environment
Preventing Contact Accidents with Materials Handling Equipment
We conduct training on operation of forklifts and tailgate lifters and install fixed barricades to prevent contact between materials handling equipment and pedestrians.
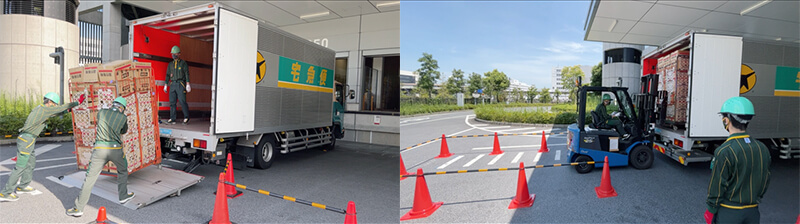
Introduction of Safety-Enhanced Equipment
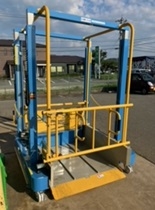
To prevent occupational accidents during materials handling operations, we have introduced safety-enhanced equipment. By fixing the operating boundary for materials handling equipment and restricting the opening of roll box pallets during raising and lowering, we aim to increase safety.
Preventing Occupational Accidents Caused by Vehicles
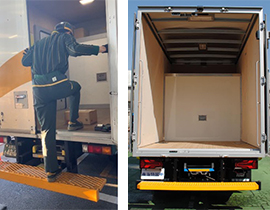
To prevent drivers from falling from the cargo decks of trucks, we are installing handholds.
We are also installing handholds on truck doors to prevent finger entrapment.
Unification of On-Premises Sign Display Rules
In order to prevent occupational accidents associated with the handling of roll box pallets and forklift work, we have clarified areas of operation for forklifts and designated safe routes for pedestrians. We have also established common standards for safe routes, areas of operation for forklifts, and lines of movement for roll box pallets —specifying details such as the colors, widths of markings, signs, and installation locations—and unified rules for signs and markings on premises.
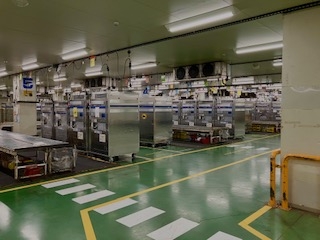
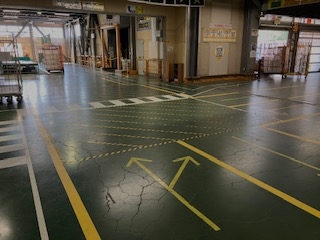
Education for Development of Professional Human Resources
Meeting Regarding Measures to Promote Occupational Safety and Health Management System
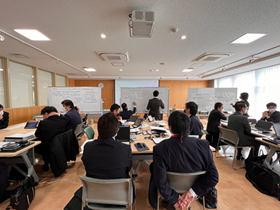
At Yamato Transport, we held meetings to exchange opinions on occupational safety and health management with some branch office managers and safety officers. We presented case studies on OSHMS implementation methods and measures to prevent recurrences of occupational accidents to increase the safety awareness of employees.
Training for Newly Appointed Operational Managers
At Yamato Transport, training for employees appointed as operational managers is conducted according to the timing of their appointment (four times per year). The training aims to increase the safety awareness of the managers by covering laws and regulations related to occupational health and safety and case studies of what happened when occupational accidents occurred.
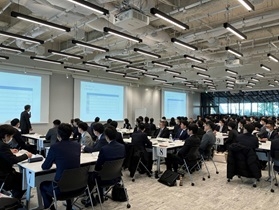
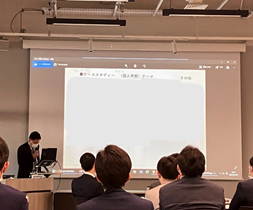
Manager Education
Yamato Transport provides education to employees who have been appointed as site managers or legal management supervisors (safety management supervisors or health management supervisors), using an internal video platform. Through case studies of internal accidents and results of supervisory inspections, legal managers can gain a deeper understanding of their own roles.
Education for Development of Professional Human Resources | FY2023 |
---|---|
Meetings regarding measures to promote the Occupational Safety and Health Management System | 336 |
Training for Newly Appointed Operational Managers | 89 |
Regular education for safety management supervisors | 4,793 |
Regular education for health management supervisors | 4,909 |
Campaigns and Initiatives for Increasing Safety Awareness
Zero Occupational Accidents Campaign
Yamato Transport conducts a Zero Occupational Accidents Campaign in conjunction with the Zero Occupational Accidents Week conducted by the Ministry of Health, Labor and Welfare. The campaign promotes self-directed activities to prevent occupational accidents at work sites, with the aim of raising safety awareness and establishing safety activities. With the goal of creating workplace environments that enable each worker to work safely and with peace of mind, the program sets out key initiatives for the entire company and engages a PDCA cycle to establish measures and promote safety and health activities. During a preparatory period in the lead up to the program, site managers and legal management supervisors refresh their knowledge of safety and understanding of their duties via e-learning.
Each day during the campaign period, they gather and share examples of occupational accidents. After the program, they are required to examine the causes of occupational accidents and measures to prevent recurrences. They aim to increase safety awareness throughout the entire company.
Safety Emphasis Day
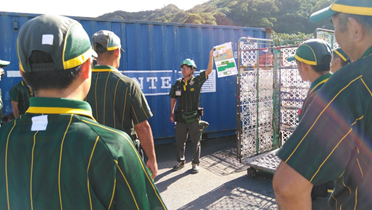
Yamato Transport has designated the third Wednesday of every month as “Safety Emphasis Day.” This is a day for all employees to review themselves to check whether they are putting safety first in their daily activities, and to take steps to prevent occupational accidents and traffic accidents, both as a company and systematically on key points for each business site. After Safety Emphasis Day, safety meetings are used to review Safety Emphasis Day initiatives.
Measures Against Heatstroke
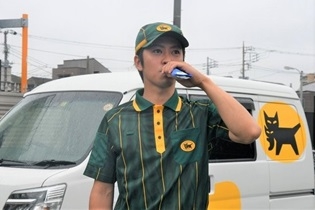
Yamato Transport has implemented various measures to suppress the onset and severity of heatstroke in daily life and during work. Specifically, we have created a more comfortable work environment by installing air coolers and spot coolers at bases and other parcel sorting locations. We have also introduced other items as measures against heatstroke, such as neck coolers, salt candies, and salt tablets for employee health management. Additionally, we have prepared guidelines and manuals on heatstroke countermeasures to alert all employees to the dangers of heatstroke and inform them about the flow of reporting when heatstroke occurs.
Group Company Safety Initiatives
Each company in the Yamato Group conducts safety initiatives suited to its own business activities. Please see the website of each company for details.